Lean Lessons in Challenging Times
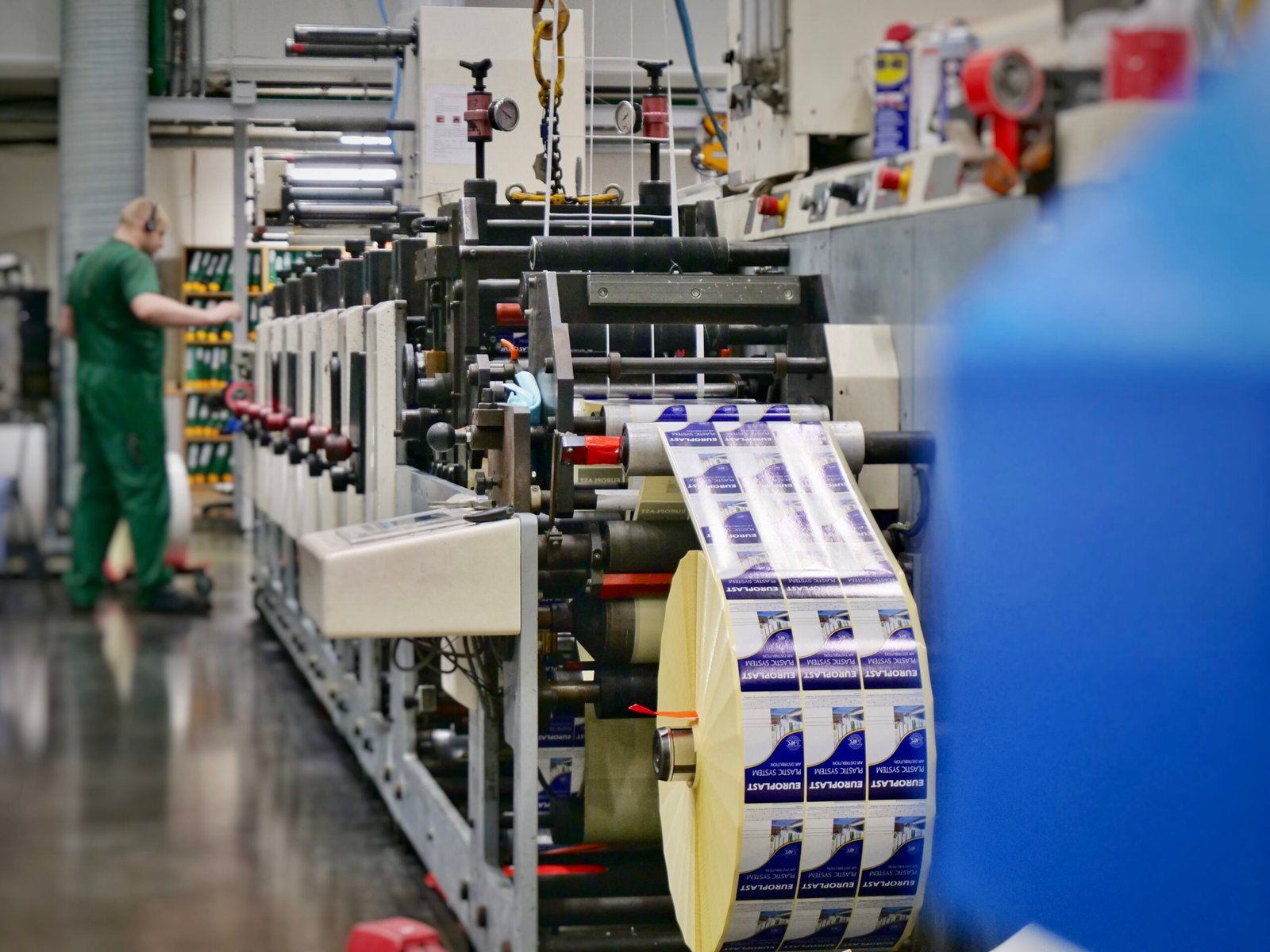
Operational Excellence – Operation based on Lean best practices that helps businesses achieve better results with fewer resources. Companies that master it strengthen their competitive advantage, and this is especially important in challenging times. As the experience of PakMarkas company shows, the benefits are immediately apparent when mastery techniques are applied, and they are really significant.
‘The point of operational excellence is to make problems visible and to solve them, to constantly look for non-value-creating processes, to eliminate them, to look for opportunities to improve existing processes, to improve and learn by ourselves,’ Deividas Akelis, Lean manager of PakMarkas UAB, describes the company’s operating philosophy.
The company of labelling and packaging solutions leading in the Baltic States started implementing operational excellence principles in 2016. The search for effective methods of operation was driven by the desire to be even closer to customers and to maximally respond to their needs, rationalize costs, and streamline activities and work processes. According to Mr. Akelis, the turn to Lean was inevitable: seeing how widespread this methodology is and what benefits it brings to companies, it is simply impossible take no regard of it and not use the merits of this factor that increase competitive advantage.
Tools Are in the Hands of All Employees
PakMarkas is a production company, and it is especially important for such companies to use time and other resources as rationally as possible. ‘We have set the goal for ourselves of producing a product that fully meets the customer’s expectations from the very first time, and the systematic application of Lean methodologies helps this a lot,’ says Mr. Akelis.
According to him, integration of these good practices into daily operations brought immediate benefits. The interviewer mentions specific results: the time of order processing has been reduced by one third – to 20 minutes; maintenance of the technical condition of equipment has improved, breakdowns occur less often; we have learned not to waste – we maintain an optimal stock of raw materials and tools. Cleanliness and tidiness are maintained in workplaces, and compliance with work safety, hygiene and standards implemented in the company, such as BRCGS, is ensured.
Another significant direction of Lean is continuous improvement of operations and elimination of non-value-creating work. We have tools for this purpose as well, and the best results are achieved when all employees are involved. At PakMarkas, they can make suggestions and create a working environment where it is comfortable and good to work, and for the implemented improvements they are motivated both with symbolic rewards and financially: the employee receives a part of the amount saved by such improvement projects.
It must be admitted that engaging all employees is not easy for most companies on the path to operational excellence. According to Mr. Akelis, the most important factors in creating a culture of continuous improvement are training, communication and the example shown by the managers. The last factor is especially important – PakMarkas’ experience shows that the level of operational efficiency is directly related to the extent to which direct managers are involved, because they are the ones who shape the culture of joint efforts and the understanding that this is the way to work in this company.
‘We have a tradition of going to work with our colleagues in production, preparation, customer service, sales and other departments on the last Friday of the month. This helps us to get acquainted with the work performed by others, to better understand the processes taking place in the company and their interconnections. By working together, we look for the causes of losses and opportunities for improvement. This practice also greatly contributes to the formation of culture,’ the representative of PakMarkas enunciates.
International Community
PakMarkas participates in the Lean in Europe programme of the EU-Japan Centre, which provides an opportunity to visit such companies as Toyota, Skoda, LEGO, BMW and many others, to see how they apply the principles of operational excellence, to get to know a like-minded community. One of the visits this September was hosted by PakMarkas – eighteen participants from various European countries representing the pharmaceutical, automotive component manufacturing, food, textile, telecommunications, IT industries looked at the practices applied in the Lithuanian company, shared their experiences, and worked in groups. Such meetings are also valuable for the company itself – Mr. Akelis is happy not only with the opportunity to welcome the distinguished delegation, but also with the opportunity to gain useful insights.
‘One of the working groups analysed product packaging, where we have a lot of manual work and incompletely elaborated processes. We received valuable advice on how to optimize workplaces and inventory, avoid additional processes, and reduce manual work. Some of the questions made me wonder why we do things the way we do. It was useful to hear how guests from other sectors solve similar challenges,’ says the PakMarkas specialist.
Professor Richard Keegan who accompanied the delegation assures that the visit left him with a great impression of excellence, especially emphasizing the contribution of PakMarkas employees to the overall cultivation of a culture of improvement.
‘It was so gratifying to observe how much significance and opportunities the company provides to its people. We can see the team understanding that change starts within each individual employee and everyone plays an important role. Their determination and enthusiasm for improving processes, as well as their willingness to openly share what worked well and what didn’t, is simply commendable. The PakMarkas team has really delved into Lean methodologies and implements them not by blindly copying, but by responsibly adapting individual tools where they will bring the most benefit in improving the company’s business processes,” says Prof. R. Keegan.
Customers Also Win
A culture of operational excellence undoubtedly has a positive effect on results, especially in challenging times, when it can be safely called a pillar of business vitality. According to Mr. Akelis, the main advantage that Lean provides to the company is the ability to do more with fewer resources. This means shorter production and delivery times, continuous improvement of product quality, and a culture of innovation. All this is a benefit for the company’s customers and an additional point in the competitiveness table.
‘The benefits of operational excellence are obvious, especially at a time when the manufacturing sector is facing spikes in energy resource prices, supply disruptions, multiply extended delivery terms for raw materials and goods, and other challenges. During the pandemic, it was not easy to ensure the continuity of Lean due to remote work and restricted access to production facilities, however, the activities started not only did not stop, but they also became a strong support at that time, especially in production,’ assures the Lean Manager of PakMarkas.