Relevant for exporters: the German deposit system is being expanded, PakMarkas prints special labels
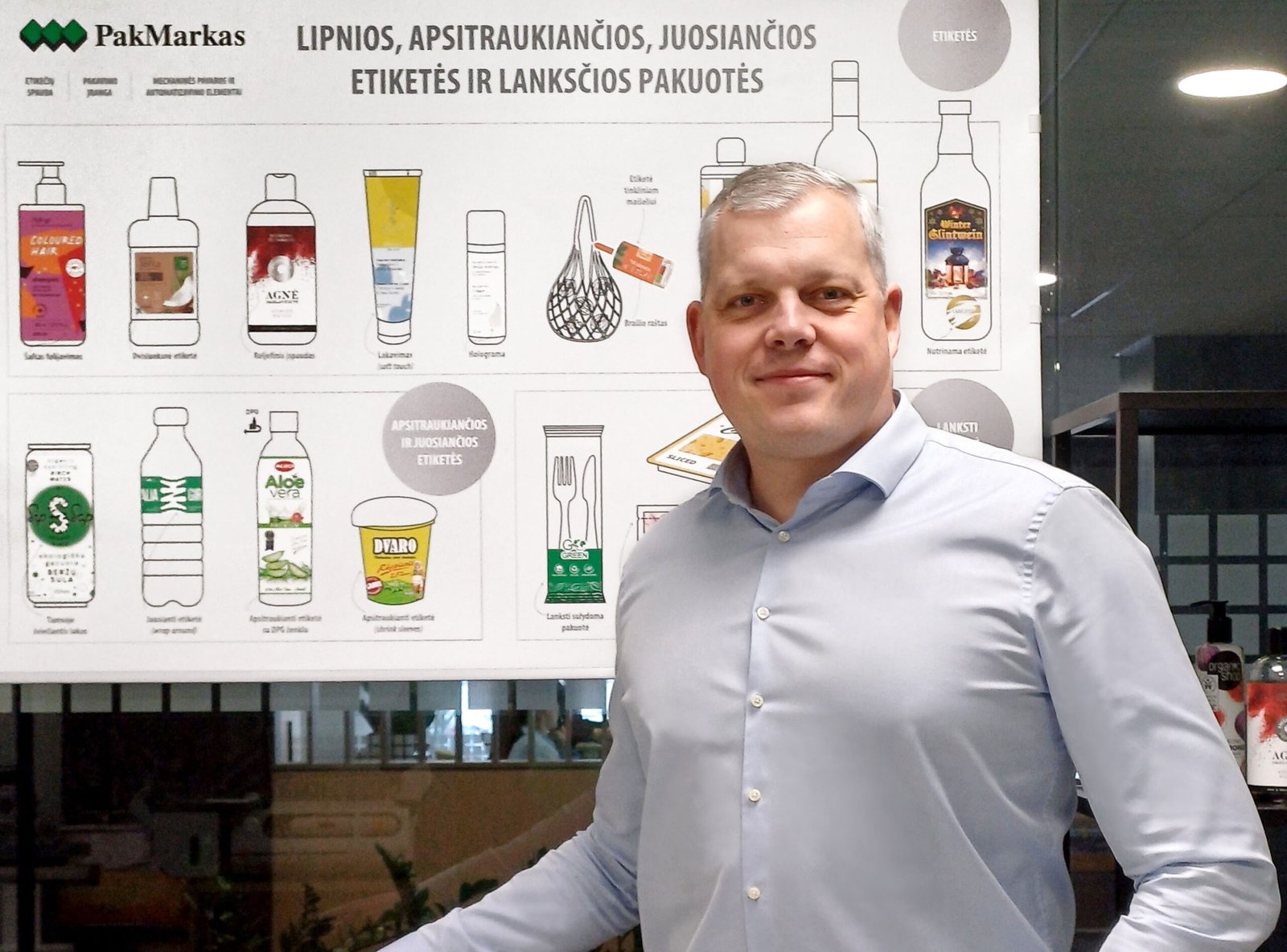
In Germany, one of Lithuania’s largest export markets, mandatory marking requirements for refundable containers are expanding: a new category of beverages is being added to the system. PakMarkas, the only company in the Baltic States with the right to print labels with the DPG deposit marking, reminds that the novelty will come into effect on the first day of 2024.
DPG (Deutsche Pfandsystem GmbH) – a container deposit system with a uniform packaging labelling standard – has been operating in Germany since 2005. The DPG marking enables the automatic scanning of single-use beverage packages, their collection and facilitates the collection of the mandatory deposit. Until now, all plastic, glass and can packaging of soft beverages and light alcoholic beverages sold in Germany have been marked with it.
“Legal labelling of containers includes DPG marking, colour and bar code with number. Labels with DPG can be printed only by companies with the appropriate certificate, ensuring that they meet all the requirements for the paints used, equipment and quality. There are not many such companies in the European Union, we are one of the few, and in the Baltic States we are the only company with the right to print labels with the DPG deposit mark,” says Miroslav Brazulevič, Head of the Product Development Department of the PakMarkas company.
Solution for already existing labels
Companies that produce juices, water and mineral water, lemonades, as well as beer and other light alcoholic beverages and import them to Germany must label their products bottled in “hard” packaging – plastic, glass bottles or cans – with the DPG marking. Starting next year, all drinkable milk products sold in plastic bottles with a volume from 0.1 to 3.0 litres will have to be labelled with the DPG marking.
“From the first day of 2024 the products will have to be labelled with the DPG marking – it will be prohibited to sell the products without it. However, the already labelled products will not be allowed to appear at the points of sale until the previously scheduled date. Until then, they can be stored in the warehouses of the importer or trader,” explains M. Brazulevič.
The entry into force of the new DPG requirements does not only mean an additional burden for German merchants, who after the end of working hours on the 31st of December will have to ensure that the plastic bottles of milk, kefir, and yogurt on the shelves were replaced by bottles bearing the DPG marking on the morning of the 1st of January. Manufacturers may also have to worry about how to deal with existing labels that are not marked in accordance with current requirements, as well as products in warehouses that already have the old labels applied.
“In order not to have to throw away already produced labels without DPG or print new ones, we would recommend to make additional, so-called DPG cover labels. They can be applied on products with labels of the old model and the products labelled in this way can be sold in accordance with all requirements,” the specialist of PakMarkas offers a solution.
DPG certification and new printing capabilities
Manufacturers and distributors affected by this novelty could register themselves and register their products, which have to be labelled, in the system since spring. They have been given special codes that have also been passed on to certified printing companies. These, having checked the provided codes in the DPG system, can print labels bearing the DPG marking.
In order for the DPG system to work smoothly and for the packaging collection machine to accurately read the marks and not return it to the user, labels with the DPG marking have special printing requirements. A company that wishes to obtain a license must go through a certification process and is audited every year. For labels, the company must use special DPG inks, intended only for the German market, to ensure the safety and control of the process. It is necessary to guarantee the high-quality printing of the DPG marking, and the compliance of the print with the requirements must be checked with the testing device of the authorized manufacturer. Such an audit in the company PakMarkas has taken place for three times.
The list of PakMarkas DPG customers includes not only Lithuanian companies, but also companies from other countries that export their products to Germany, as well as German companies that sell their products on the local market. Depending on the need, PakMarkas prints the DPG marking on adhesive, shrink sleeve and wrap-around labels. After installing modern printing equipment this summer, the company almost doubled its shrink-sleeve label printing capacity.
“We can offer our customers shrink sleeve labels, which can have up to 10 colours and are printed on probably the thinnest 30-micron PET material available on the market. The new device, like other printing devices used in our company, is equipped with an automatic print quality control system, which helps to avoid printing errors and reduce the amount of waste,” M. Brazulevič reveals the advantages of label printing equipment.