The supply of raw materials for labels has been disrupted – what manufacturers shall do
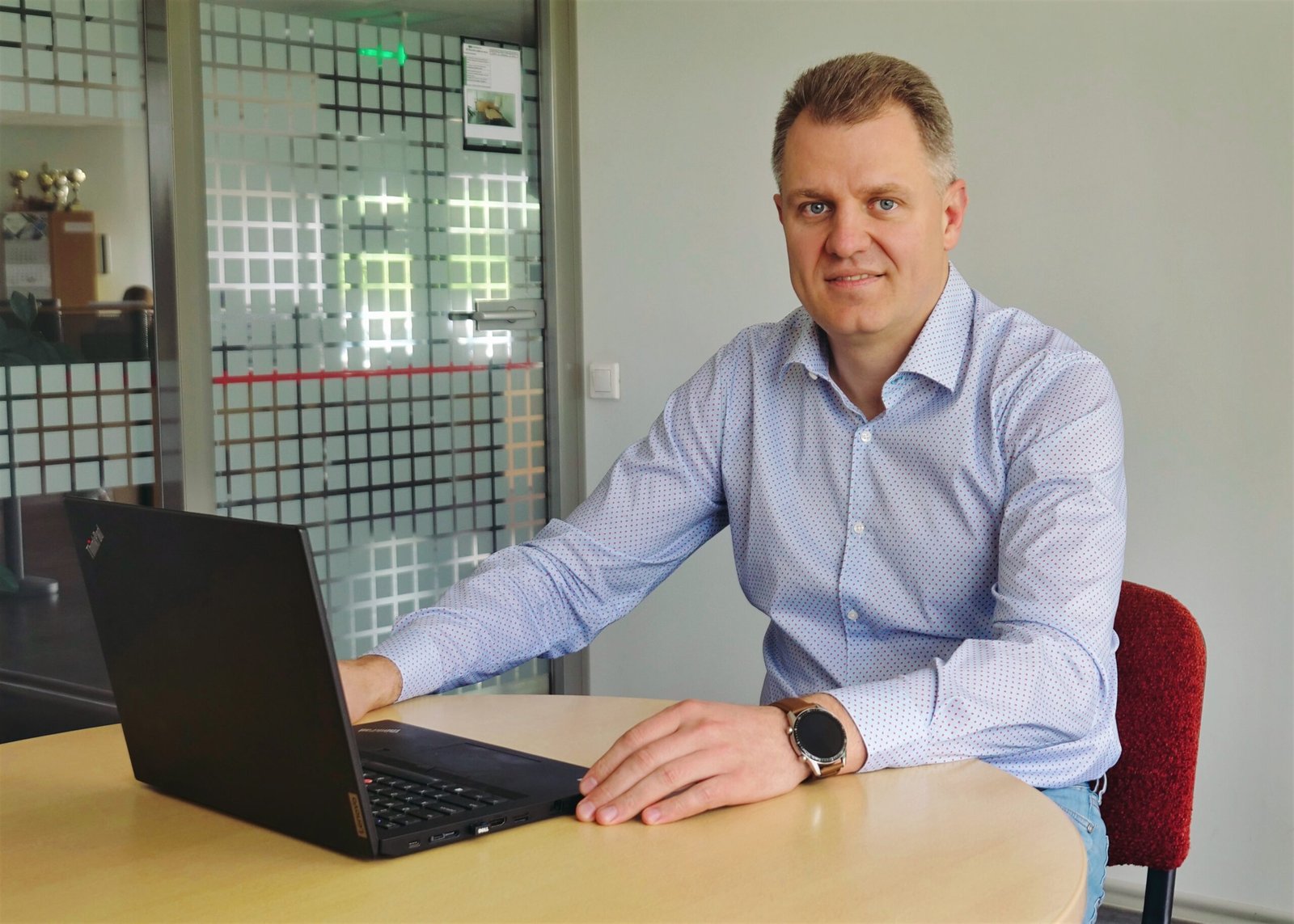
A recent strike at the large supplier’s factory disrupted the supply of raw materials needed to manufacture product packaging, and the war pushed up prices even further. PakMarkas, the company of packaging and labelling solutions, recommends that manufacturers take the situation seriously and plan production responsibly, and the company itself has taken steps to ensure the smoothest possible customer service.
The shortage of raw materials and extended deadlines for their supply are putting pressure on manufacturers in all areas: it is difficult to obtain not only components or raw materials for product manufacturing, but also the supply of materials needed for the manufacturing of labels has been disrupted. This can have a significant impact on product sales: even if the product itself can be manufactured without interruption, its logistics and delivery to store shelves requires packaging with a product label.
UPM Raflatac, one of the world’s largest manufacturers of label and packaging raw materials, was shut down for four months due to a workers’ strike. As it was the pulp manufacturing branch gone on strike, the supply of paper-related raw materials was most affected. There is a shortage of special siliconized paper on the market, which is used as a basis for adhesive labels,” says Donatas Burba, Head of Print Sales at PakMarkas.
Alternative solutions
The consequences of the strike rolled over the entire supply chain: the delivery time for raw materials increased dramatically – if earlier the order used to come in a week, now we had to wait as much as 5-6 months. Prices of raw materials also rose, and their growth was further accelerated by the outbreak of war in Ukraine. Manufacturers used to purchase low-price wood for pulp production from Russia and Belarus, now they have to concentrate on other markets where prices are quite different.
According to Mr. Burba, the situation is quite paradoxical – not the material for the entire label is missing, but for one component of the adhesive label “sandwich”, however, this lack has disrupted the whole process of labelling the packaging. Siliconized paper is a so-called ‘carrier’ material – it ensures that the ‘face’ of the label can be properly printed, cut out in a proper shape and properly attached to the product’s primary packaging during the labelling process.
The plant of UPM Raflatac resumed operations in May, but supply of raw materials may take up to half a year, until manufacturing returns to normal. Therefore, PakMarkas has started to look for ways to replace siliconized paper while maintaining all the quality properties of the label.
“An alternative ‘carrier material’ is PET. The change of raw material has no effect on the appearance or quality of the label, as the label remains the same, only the base on which it is affixed changes. There are some differences in the manufacturing process, especially if non-smart equipment is used, but they are not difficult to resolve. The most important thing is that this solution allows to produce adhesive labels quickly, without disrupting the labelling stage,” says an expert from PakMarkas.
Preventing possible supply disruptions, the company also significantly increased its stock of raw materials. So at the moment, customers no longer have to wait for the necessary raw materials, they should suffice until the beginning of winter.
Preventing the problem
Daumantai LT, the manufacturer of tomato sauces, ketchups and mayonnaise, has felt the tension in the pulp industry for a long time. According to Virmantas Pikelis, Head of Daumantai LT’s Supply and Logistics Division, the industry was severely affected by the pandemic and the war, and the UPM Raflatac strike threatened to become the last drop in the cracking supply.
“The situation was unenviable – although rising prices had already become almost a daily routine, when a large manufacturer stopped its operations, it became unclear whether it would be possible to get raw materials at all and how long such a break would last. It’s good that we heard about such threats from PakMarkas when we had time to prepare, and not when attaching the last batch of labels,” he says.
Daumantai LT took advantage of the offer to use an alternative material for the label if necessary, adjusted its equipment and tested it – printed several product batches with labels of a different composition. And although so far it is still possible to work with stocks of siliconized paper, according to Mr. Pikelis, the company is fully prepared for Plan B in case of any surprises. And anything can happen, because even after the resumption of UPM Raflatac operation, it is difficult to predict how long it will take the imbalance between market supply and demand developed over the past few months to return to normal.
“In the general context of a shortage of raw materials and breaking logistics chains, the packaging label seems to be a small enough component, but it is far from being the true. You can have both raw materials and packaging, be ready for manufacturing, but you just won’t put it on the market without a label. It is just as important component as any other raw material,” emphasizes Mr. Pikelis.
Planning ahead
The market, which is accustomed to working with ‘just-in-time’ delivery deadlines, is now facing a rapid reorientation. According to Donatas Burba, sales specialist of PakMarkas, some manufacturers have assessed the situation accordingly and have already ordered raw materials for the next six months or even longer. ‘Planning, planning, planning’ would be expert’s advice for those who want production to run smoothly. According to him, PakMarkas does everything to secure the most stable supply of raw materials for the longest possible period, but working with the accumulated raw material residues in the warehouse provides less flexibility.
“It is important to understand that the amount of raw materials available here and now is limited. Therefore, if the manufacturer wants a large and unordered quantity, we may have to wait for a new shipment of the raw materials we have ordered to arrive. So if in the past the market was used to increase size of orders to get a better price, it is now normal to plan for smaller quantities, but much ahead. On the other hand, it is easier to secure stocks of standard, commonly used raw materials, and PakMarkas has accumulated the largest stocks of them,” comments the expert.